Литейная технология – это процесс получения литых заготовок путем заливки расплавленного металла в формы, полость которых повторяет конфигурацию отливки. При охлаждении металл отвердевает и принимает конфигурацию полости формы. Литьем получают разнообразные конструкции отливок массой от нескольких грамм до 300т, длиной от нескольких сантиметров до 20м, со стенками толщиной 0,5-500 мм(блоки цилиндров, поршни, коленчатые валы, корпуса и крышки редукторов, зубчатые колеса, станины станков, станины прокатных станов, турбинные лопатки и т.д.). Отливки получают из черных сплавов (чугуны, стали) и цветных сплавов(алюминиевых, магниевых, медных, цинковых, титановых и др.). Для получения расплава применяют шихтовые материалы: - небольшие слитки металлургического производства (чушки) - отходы собственного производства - лом - флюсы Различные сплавы имеют разные литейные свойства, которые характеризуются следующими параметрами: 1)Жидкотекучесть - это способность металлов и сплавов течь в расплавленном состоянии по каналам литейной формы, заполнять её полости и чётко воспроизводить контуры отливки. Жидкотекучесть литейных сплавов зависит от температурного интервала кристаллизации, вязкости и поверхностного натяжения расплава, температуры заливки и формы, свойств формы и т. д. Чистые металлы и сплавы, затвердевающие при постоянной температуре (эвтектоидные сплавы), обладают лучшей жидкотекучестью, чем сплавы, образующие твёрдые растворы и затвердевающие в интервале температур. Чем выше вязкость, тем меньше жидкотекучесть. С увеличением поверхностного натяжения жидкотекучесть понижается и тем больше, чем тоньше канал в литейной форме; с повышением температуры заливки расплавленного металла и температуры формы жидкотекучесть улучшается. Увеличение теплопроводности материала формы снижает жидкотекучесть. Так, песчаная форма отводит теплоту медленнее, и расплавленный металл заполняет её лучше, чем металлическую форму. Наибольшей жидкотекучестью обладает серый чугун, наименьшей - магниевые сплавы.
2) Усадка - Свойство литейных сплавов уменьшать объём при затвердевании и охлаждении. Усадочные процессы в отливках протекают с момента заливки расплавленного металла в форму вплоть до полного охлаждения отливки. Различают объёмную и линейную усадку, выражаемую в относительных единицах.
Линейная усадка - уменьшение линейных размеров отливки при её охлаждении от температуры, при которой образуется прочная корка, способная противостоять давлению расплавленного металла, до температуры окружающей среды. Линейную усадку определяют соотношением, %:
где lф и lотл – размеры полости формы и отливки при температуре 20°C.
На линейную усадку влияют химический состав сплава, температура его заливки, скорость охлаждения сплава в форме, конструкция отливки и литейной формы. Так, усадка серого чугуна уменьшается с увеличением содержания углерода и кремния. Усадку алюминиевых сплавов уменьшаем повышение содержания кремния. Усадку отливок уменьшает снижение температуры заливки. Увеличение скорости отвода теплоты от залитого в форму сплава приводит к возрастанию усадки отливки.
При охлаждении отливки происходит механическое и термическое торможение усадки. Механическое торможение возникает вследствие трения между отливкой и формой. Термическое торможение обусловлено различными скоростями охлаждения отдельных частей отливки. Сложные по конфигурации отливки подвергаются совместному воздействию механического и термического торможения.
Линейная усадка для серого чугуна составляет 0,9-1,3%, для высокопрочного чугуна до 1.7%, для ковкого чугуна …%, для углеродистых сталей 2-2,4%, для алюминиевых сплавов 0,9-1,5%, для медных 1,4-2,3%.
Объёмная усадка - уменьшение объёма сплава при его охлаждении в литейной форме при формировании отливки. Объёмную усадку определяют соотношением, %:
г
де Vф и Vотл – объем полости формы и отливки при температуре 20°C. Объемная усадка приблизительно равна утроенной линейной усадке.
Усадка в отливках проявляется в виде: усадочных раковин - сравнительно крупных полостей, расположенных в местах отливки, которые затвердевают последними; (На рис.2 показан процесс образования усадочной раковины в отливке.) усадочной пористости - скопление пустот, образовавшихся в отливке в обширной зоне в результате усадки в тех местах отливки, которые затвердели последними без доступа к ним расплавленного металла; трещин; короблений - изменение формы и размеров отливки под влиянием напряжений, возникающих при охлаждении.
Существует несколько способов изготовления отливок. Перечислим основные из них : литье в песчаные формы(ПФ), литье в кокиль(К), литье по выплавляемым моделям(ВМ), литье под давлением(Д).
Литье в песчаные формы.
1.Сущность процесса заключается в изготовлении отливок свободной заливкой расплавленного металла в песчаную форму. После затвердевания и охлаждения отливки осуществляется ее выбивка с одновременным разрушением формы.
2.Материалы и оснастка. 1)Песчаная форма(ПФ) – разовая литейная форма, изготовленная из уплотненной формовочной смеси. ПФ состоит из двух полуформ. Для образования отверстий применяются песчаные стержни.
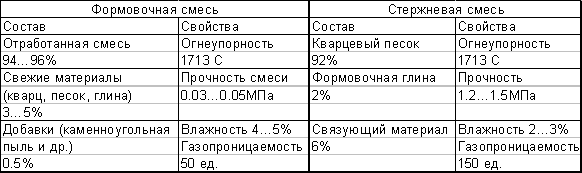
2)Типовые составы формовочных и стержневых смесей. 3)Модельный комплект : модель детали, модели элементов литниковой системы, модельные плиты, стержневые ящики. 4)Опоки.
3.Основные технологические операции.
1)Изготовление полуформ по модельным плитам(наиболее распространенными способами уплотнения смеси при машинной формовке являются прессование, встряхивание и их сочетание). 2)Изготовление стержней. 3)Сборка формы с простановкой стержней и подготовка ее к заливке. 4)Заливка форм расплавленным металлом. 5)Затвердевание и охлаждение отливок. 6)выбивка отливок из форм и стержней из отливок. 7)отделение литниковой системы от отливок, их очистка и зачистка. 8)контроль качества отливок.
Возможные дефекты отливок, причины и меры по их устранению.
1)Недоливы и спаи. Образуются от неслившихся потоков металла, затвердевающих до заполнения формы. Возможные причины: холодный металл, питатели малого сечения. 2)Усадочные раковины – закрытые внутренние полости в отливках с рваной поверхтностью. Возникают вследствие усадки сплавов, недостаточного питания. Устраняют с помощью прибылей. 3)Горячие трещины в отливках возникают в процессе кристаллизации и усадки металла при переходе из жидкого состояния в твердое при температуре, близкой к температуре солидуса. Склонность сплава к образованию горячих трещин увеличивается при наличии неметаллических включений, газов, серы и других примесей. Образование горячих трещин вызывают резкие перепады толщин стенок, острые углы, выступающие части. Высокая температура заливки также повышает вероятность образования горячих трещин.
Для предупреждения образования горячих трещин в отливках необходимо обеспечивать одновременное охлаждение толстых и тонких частей отливок; увеличивать податливость литейных форм; по возможности снижать температуру заливки сплава.
4)Пригар – трудноудаляемый слой формовочной или стержневой смеси, приварившийся к отливке. Возникает при недостаточной огнеупорности смеси или слишком большой температуре металла. 5)Песчаные раковины – полости в теле отливки, заполненные формовочной смесью. Возникают при недостаточной прочности формовочной смеси. 6)Газовые раковины –полости отливки округлой формы с гладкой окисленной поверхностью. Возникают при высокой влажности и низкой газопроницаемости формы. 7)Перекос. Возникает из-за неправильной центровки.
4.Область применения.
Применяют во всех областях машиностроения. Получают отливки любой конфигурации 1…6 групп сложности. Точность размеров соответствует 6…14 группам. Параметр шероховатости Rz=630…80мкм. Можно изготавливать отливки массой до 250т. с толщиной стенки свыше 3мм.
5.Преимущества.
- конфигурация 1…6 групп сложности - возможность механизировать производство - дешевизна изготовления отливок - возможность изготовления отливок большой массы - отливки изготовляют из всех литейных сплавов, кроме тугоплавких
6.Недостатки.
- плохие санитарные условия - большая шероховатость поверхности - толщина стенок > 3мм - вероятность дефектов больше, чем при др. способах литья.
Литье по выплавляемым моделям.
1.Сущность процесса заключается в изготовлении отливок заливкой расплавленного металла в тонкостенные, неразъемные, разовые литейные формы, изготовленные из специальной огнеупорной смеси по разовым моделям. Разовые выплавляемые модели изготовляют в пресс-формах из модельных составов. Перед заливкой модель удаляется из формы выплавлением, выжиганием и т.д. Для устранения остатков модельного состава и упрочнения форма нагревается и прокаливается. Заливка осуществляется в разогретые формы для улучшения заполняемости.
2.Материалы и оснастка. 1)Модельная форма состоит из модельного состава(парафин, стеарин, церезин, канифоль и т.д.). 2)Формовочная смесь : 2ч. пылевого кварца, 1ч. связующего материала. 3)Пресс-форма для изготовления моделей. 4)Литейная форма. 5)Вибрационная установка.
3.Основные технологические операции изготовления форм и отливок. 1)Приготовление модельного состава. 2)Изготовление моделей отливки и элементов литниковой системы или секции моделей. 3)Сборка моделей или секций моделей в блоки. 4)Изготовление литейной формы. 5)Подготовка литейных форм к заливке и заливка металла в горячую форму. 6)Затвердевание и охлаждение отливки в форме. 7)Снятие формы с отливки.
4.Область применения. Этим способом можно отливать изделия из различных сплавов любой конфигурации 1…5 групп сложности массой от нескольких грамм до 250кг с толщиной стенок от 1мм. Припуск на механическую обработку составляет 0.2-0.7мм. Применяется в различных областях машиностроения.
5.Преимущества. - Можно получать отливки из тугоплавких изделий. - Получают конфигурации отливок 1…5 групп сложности. - Высокая точность геометрических размеров и малая шероховатость поверхности.
6.Недостатки.
- длительность процесса - дороговизна
Литье в кокиль.
1. Сущность процесса заключается в изготовлении отливок из жидкого расплава свободной его заливкой в многократно используемые металлические формы – кокили, обеспечивающие высокую скорость затвердевания жидкого расплава и позволяющие получать в одной форме от нескольких десяток до нескольких тысяч отливок.
2. Материалы и оснастка. 1)форма отливки – кокиль 2)расплавленный металл 3)теплоизоляционное покрытие
3. Последовательность изготовления отливок. 1)Подготовка кокиля к работе : очистка от остатков теплоизоляционного покрытия, нагрев до температуры 150-200° и нанесение свежего слоя теплоизоляционного покрытия толщиной 0,1…0,5мм, а на литниковые каналы и прибыли до 1мм. 2)Сборка кокиля : установка стержней, соединение частей кокиля. 3)Заливка расплавленного металла в кокиль. 4)Затвердевание и охлаждение отливки. 5)Удаление из отливки металлических стержней (если они есть) после образования в ней достаточно прочной корки. 6)Извлечение отливки из кокиля после ее охлаждения до температуры 0,6…0,8 от температуры солидуса. 7)Охлаждение или подогрев кокиля до оптимальной температуры 200-300°С и подкраска (при необходимости) рабочей поверхности кокиля.
4.Область применения. Применяют в автомобиле и танкостроении. Литьем в кокиль изготавливают отливки из чугуна, стали и цв. сплавов. Трудно получить сложные стальные отливки ввиду значительной усадки литейных сталей, что ведет к образованию трещин (в отсутствии податливости формы). Целесообразно применять в серийном, крупносерийном и массовом производствах. Этим способом изготавливают отливки из стали массой до 160кг., из цв. сплавов – до 50кг. с толщиной стенок от 3 до 100мм. Точность размеров соответствует 4…12 классам. Можно изготавливать отливки 1…5 группы сложности. Параметр шероховатости поверхности Rz = 80…20мкм.
5.Преимущества. - повышенная точность геометрических размеров (по сравнению с литьем а ПФ) - снижение шероховатости поверхностей отливок (по сравнению с литьем а ПФ) - снижение припусков на механическую обработку на 10-20% - лучше санитарно-гигиенические условия - мелкозернистая структура отливок ( > прочность)
6.Недостатки. - сложность изготовления кокилей, их ограниченный срок службы (особенно при литье черных сплавов) - неподатливость кокиля и металлических стержней - затруднен вывод газов из полости формы
Литье под давлением.
1.Сущность процесса заключается в получении отливок путем заливки расплавленного металла в металлическую форму (пресс-форму) под принудительным внешним давлением от 30 до 100Мпа. Конечное давление на расплав может достигать 490Мпа. Давление снимается после полного затвердевания отливки в пресс-форме.
2.Материалы и оснастка. 1)пресс-форма 2)смазка (машинное масло) 3)прессующая машина
3.Основные технологические операции. 1)Очистка пресс-формы. 2)Нагрев пресс-формы до 120…220°С и покрытие поверхности смазкой. 3)Сборка пресс-формы. 4)Залив расплавленного металла в камеру прессования и запрессовка расплава под давлением в полость пресс-формы. 5)Охлаждение и затвердевание отливки под внешним давлением. 6)После затвердевание отливки внешнее давление снимается и извлекается отливка.
4.Область применения. Используется для изготовления отливок цветных металлов сложной конфигурации с тонкими стенками массой до 45кг. Применяется в машиностроении.
5.Преимущества. - получают сложные тонкостенные отливки - низкая шероховатость поверхности, следовательно, снижается механическая обработка отливок на 90-95% - высокая точность геометрических размеров - мелкозернистая структура - улучшенные санитарно-гигиенические условия
6.Недостатки. - высокая стоимость пресс-формы, сложность ее изготовления - наличие газовоздушной пористости - ограничение номенклатуры получения отливок по размерам и массе.
|